Vznikla první ocel bez využití fosilních paliv
Výroba oceli je v současnosti relativně náročná na emise skleníkových plynů – při výrobě každé tuny oceli se nyní do ovzduší uvolní dvě tuny oxidu uhličitého (CO2). Vzhledem k množství oceli, které se vyrobí a spotřebuje po celém světě, se vůbec nejedná o zanedbatelné množství, celkově je výroba oceli zodpovědná asi za 7 % světových emisí skleníkových plynů.
Dekarbonizovat tento obor, tedy přejít od spalování fosilních paliv k jiným technologiím, je přitom velmi složité. Všechny kroky zpracování železné rudy a její přeměny v ocel totiž vyžadují velké množství energie a vysoké teploty.
Tři švédské firmy se rozhodly tento problém vyřešit společnými silami. Jedná se o těžební firmu LKAB, která vlastní největší důl na železnou rudu na světě umístěný v Kiruně, energetickou firmu Vattenfall a ocelářskou firmu SSAB. Konsorcium těchto firem nazvané Hybrit postavilo ve městě Luleå prototyp továrny na bezemisní ocel a nyní dodalo první várku této oceli automobilce Volvo. Jak tedy tyto firmy vyřešily výrobu oceli bez fosilních paliv?
Jak vyrobit ocel bez uhlí
Zjednodušený proces výroby oceli je následující:
První krok po vytěžení železné rudy je z této rudy vytvořit tzv. pelety, tedy malé kuličky. To je důležité pro jejich použitelnost ve vysokých pecích v druhém kroku, aby mezi kousky železné rudy mohl volně proudit vzduch, a zároveň aby pec neucpaly. Tyto pelety se vyrábí tak, že se z železné rudy nejprve mechanicky vytvoří kuličky, které se potom v peci vypálí, což jim dodá potřebnou tvrdost.
V současnosti se v pecích pro výrobu pelet dosahuje požadovaných teplot spalováním fosilních paliv, nejčastěji uhlí či zemního plynu. Konsorcium Hybrit v tomto kroku místo fosilních paliv používá syntetická paliva vzniklá z biomasy.
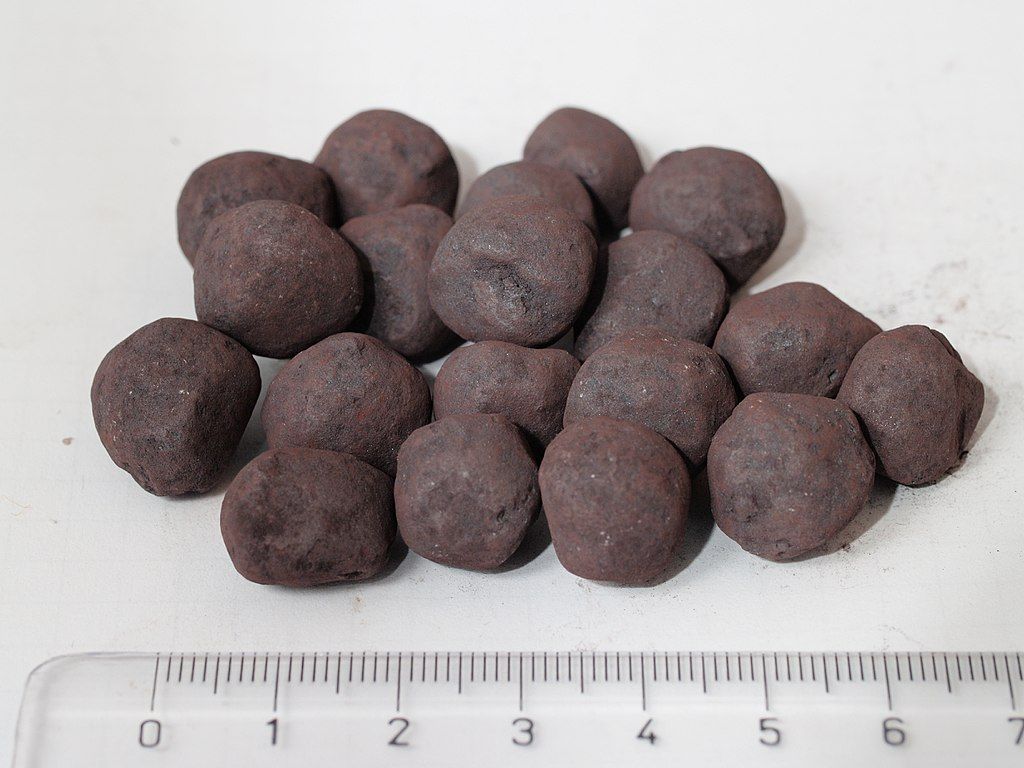
Ve druhém kroku je pak potřeba ze železné rudy (Fe3O4 nebo Fe2O3) získat čisté železo (Fe). Tomuto procesu odstranění kyslíku z chemických vazeb se říká redukce a v současnosti probíhá sléváním ve vysokých pecích za přítomnosti uhlí. Uhlík (C) z uhlí se za vysokých teplot navazuje na kyslík (O2) ze železné rudy, tvoří přitom oxid uhličitý (CO2), který uniká do atmosféry, a zůstává železo (Fe) obohacené o několik procent uhlíku.
Hybrit pro redukci železné rudy používá vodík (H2), který se za vysokých teplot váže na kyslík (O2) v železné rudě, jako vedlejší produkt vzniká voda (H2O) a zůstává čisté železo. Pro zachování bezemisního procesu je vodík vyráběn přímo na místě elektrolýzou vody s využitím elektřiny z obnovitelných zdrojů.
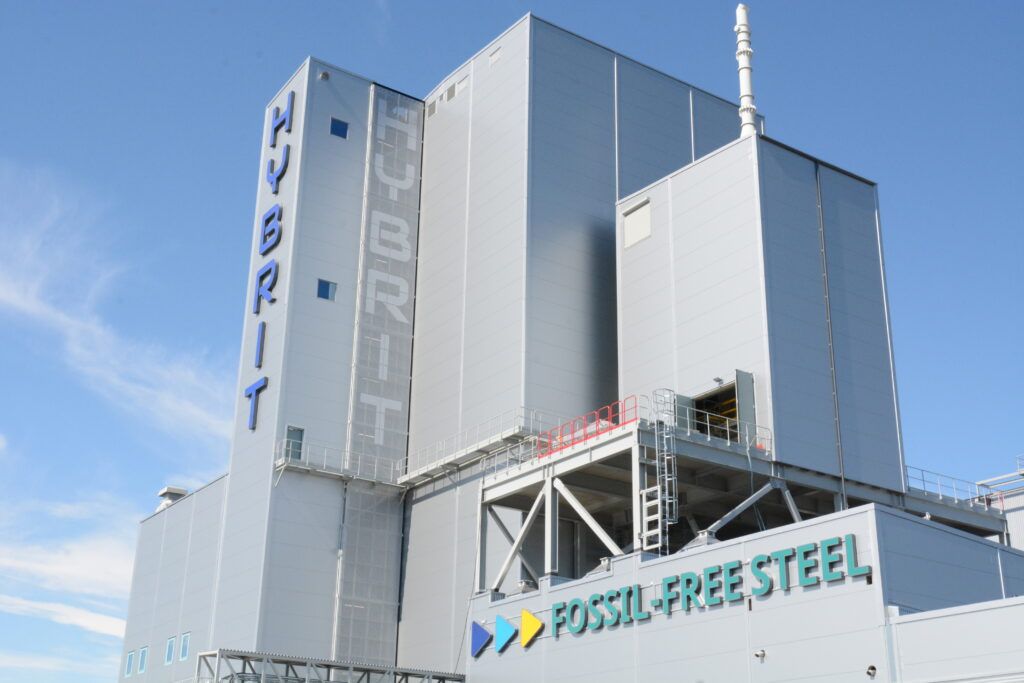
Třetí krok je vytvoření samotné oceli. Ocel je železo s příměsí uhlíku a dalších aditiv, podle způsobu použití. Železo pocházející z klasického procesu s využitím uhlí už příměs uhlíku má, avšak většinou je tento podíl příliš vysoký (okolo 4 %), ocel potřebuje mít obsah uhlíku zhruba do 2 %. V posledním kroku se pak tedy obsah uhlíku snižuje tím, že se opět za vysokých teplot na roztáté železo fouká čistý kyslík (O2), který se navazuje na uhlík (C) ve směsi a uniká do atmosféry opět jako oxid uhličitý (CO2).
Železo vzniklé bezfosilním sléváním žádnou příměs uhlíku nemá, a proto se do něj uhlík musí přidat. Tento uhlík může pocházet z biomasy, ale je možné ho získat i z fosilního uhlí, protože zde nedochází k jeho spalování (a tedy uvolňování oxidu uhličitého). Svým způsobem se také jedná o úložiště uhlíku, protože uhlík zachycený v oceli v ní zůstane prakticky navždy, v budoucnu je pak tedy možné uvažovat o tomto procesu jako o jednom ze způsobů ukládání uhlíku.
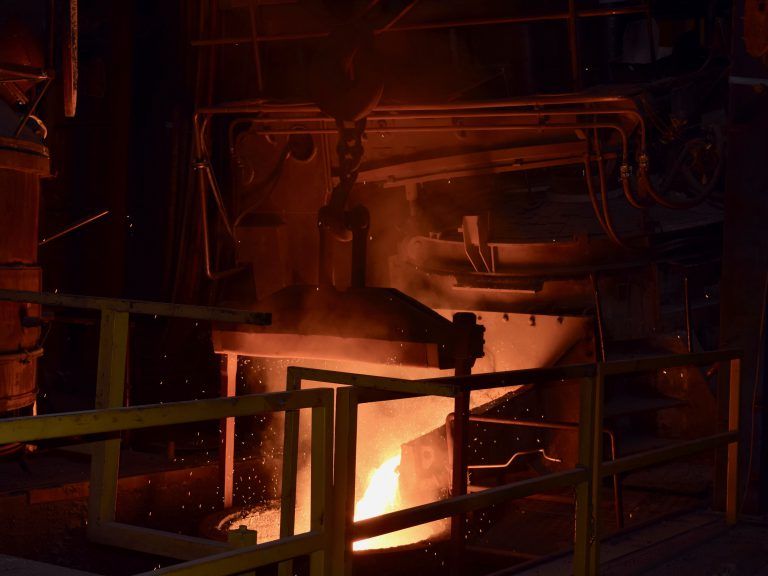
Kdy se zelená ocel vyplatí?
V současnosti není výše popsaný bezemisní proces ekonomicky výhodný vůči klasickému procesu s využitím uhlí, a to hned z několika důvodů. Hlavním důvodem je vysoká cena zeleného vodíku, který se vyrábí elektrolýzou za využití energie z obnovitelných zdrojů. Současně ale také tento proces musí konkurovat levnému uhlí a procesu, který je zavedený a optimalizovaný po dlouhá léta.
Pro to, aby se ocel mohla začít vyrábět bezemisním způsobem bez výrazného nárůstu ceny oceli je nejprve nutné snížení ceny elektřiny z obnovitelných zdrojů a snížení ceny zeleného vodíku. Zároveň musí dojít ke zvýšení ceny uhlí (případně emisí oxidu uhličitého), aby byly ocelárny finančně motivované přejít k novému procesu. Podle analytické společnosti McKinsey by se bezemisní proces výroby oceli měl začít finančně vyplácet oproti klasickému procesu mezi lety 2030-2040.
Společnost Hybrit, podobně jako další firmy, chce do té doby připravit a vyladit potřebné technologie. V prototypové slévárně, která je nyní v provozu, tak plánuje zkoušet různé procesy a hledat jejich optimalizace. Vyrábět ocel v průmyslovém měřítku a dodávat ji do švédských firem pravidelně firma plánuje v roce 2025.
Zdroj: Tisková zpráva společnosti Hybrit
Úvodní obrázek: Piqsels, CC0